Topics
トピックス
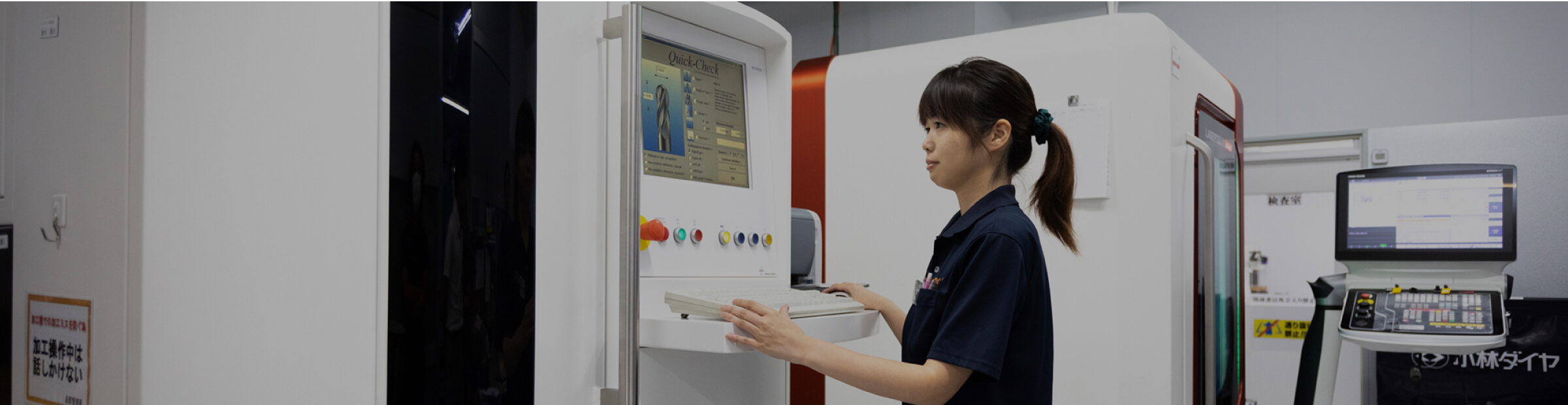
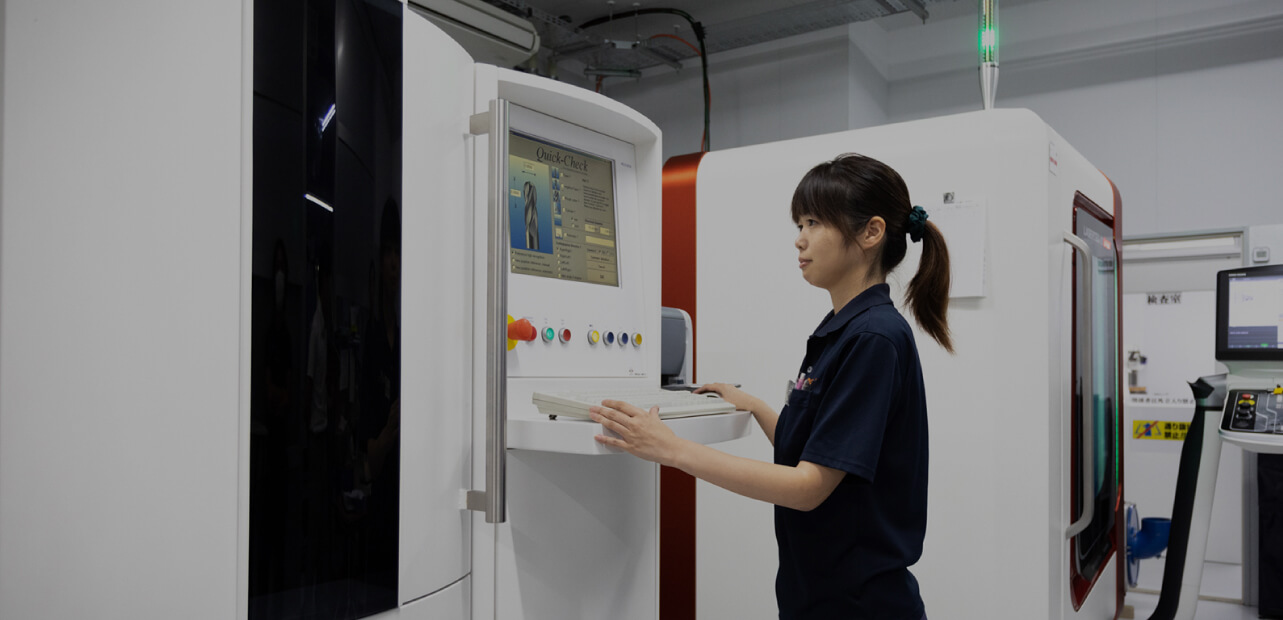
Topics
トピックス
ダイヤ工具はコストが高い!?~導入後2年で削減比50%、5年で約120万円削減が可能になった例~
技術コラム | 2022.03.19
当社はダイヤモンド切削工具の専門メーカーとして、約半世紀に渡り、製造・再研磨を行っております。
切削工具にも様々ありますが、ダイヤ工具をお使いではないお客様からは、「ダイヤ工具は高いから・・・」というお声をいただくことがあります。
ダイヤ工具が超硬工具やハイス工具に比べて価格が高いのは事実です。
小林ダイヤでは、お客様のご要望をお聞きしながら、刃先に使用するダイヤチップ(PCDチップ)の素材や形状、台金の素材を選択して設計するため、コストを抑えながらダイヤ工具が製作できます。
全ての被削材にダイヤ工具が適しているわけではありませんが、アルミ材や樹脂系材料の加工は、ダイヤ工具が得意とするところです。
ちなみに、スチールやステンレス等の鋼材加工には超硬工具が向いていて、ダイヤ工具は不向きです。
被削材や加工条件によって、適材適所の使い分けが肝要です。
さて、そのアルミ材や樹脂系材料に対しては、ダイヤ工具は超硬工具と比較して【加工距離・加工点数の増加】、【加工仕上げ面の向上】が見られるなど、多くのメリットがあります。
たしかにダイヤ工具は、超硬工具に比べてイニシャルコスト(初期投資費用)が高いことは事実です。
しかし、工具が寿命を終えるまでのランニングコスト(維持費・使用費)も含めた総額で考えますと、【次の再研磨に出すまでの加工点数の増加】と【工具の交換頻度の減少】、更に【交換にかかる人的コストの削減】が見込めますから、【結果的に超硬工具より安価に済む】ことがあります。
これを実際に経験され、メリットを享受されたユーザー様は、『もう超硬工具には戻れない!』とおっしゃっていただけます。
貴社もダイヤ工具のメリットを味わってみませんか?
ダイヤ工具と超硬工具のコストを比較した一例をご紹介します。
当社は、チップソー・ドリル・エンドミルなど様々な形状のダイヤ工具を製作していますが、ここでは、【従来は超硬チップソーを使用していたアルミ加工メーカー様の情報】をご紹介します。
要点を先にお伝えしますと、弊社のダイヤチップソーに変更していただくと、超硬チップソーと比較して、2年で削減比約50%、5年で金額にして約120万円の削減が可能でした。
細かな金額をお伝えすることが難しく、あくまで一例ですが、当社が提案したダイヤチップソーと、それまで使用されていた超硬チップソーの使用状況をまとめましたので、ぜひご覧ください。
【ダイヤチップソー提案前の状況】
・使用工具 超硬チップソー
・次回再研磨までの使用期間(ライフ) 約10日間
・年間新品購入枚数 9枚
・年間再研磨回数 45回
※補足
超硬チップソーを次の再研磨に出すまでの使用期間は約10日間。工具交換は1ヶ月で約3回実施している。
超硬チップソーの再研磨納期は、業者に依頼した後に自社へ戻ってくるまで約1ヶ月かかる。
超硬チップソーの必要在庫数は4枚。(1ヶ月辺り3枚交換+再研磨納期が長いため予備1枚)
次に、当社があるアルミ加工メーカー様へダイヤチップソーを提案し、実際に1年余りを使用していただいた結果は、以下の通りです。
【小林ダイヤ提案のダイヤチップソー】
・提案工具 ダイヤチップソー
・次回再研磨までの使用期間(ライフ) 約3ヶ月
・年間新品購入枚数 2枚
・年間再研磨回数 2回
当社のダイヤチップソーは、なんと約3ヶ月、交換せずに加工し続けることができました。
約3ヶ月後に外され、新たなダイヤチップソーに付け替えていただき、外されたダイヤチップソーは当社が再研磨し、またお返ししました。
ダイヤチップソー2枚の在庫を3ヶ月毎に交換していただきましたので、新品の購入枚数は2枚、再研磨回数も年間たった2回(各1回)で済ませることが出来ました。
なお、当社が使用済みダイヤチップソーをお預り後、再研磨してお返しするまでの期間は約2週間と、早期対応が可能です。
万一、使用中のダイヤチップソーにトラブルが発生しても、再研磨を終えたダイヤチップソーを早々にお返ししていますので、こちらに交換して加工を継続することが可能です。
この結果を、年間のイニシャルコスト・ランニングコストの合計額で比較したところ、ダイヤチップソーが超硬チップソーに対して、1年目のコスト削減率は約18.6%、2年目のコスト削減率は約50%、3年目も継続して約50%以上のコスト削減が可能でした。
1年目は、ダイヤチップソー2枚の新品購入費がかかったため削減率は低めですが、新品購入が必要ない2年目・3年目は、約50%という高い削減率を得ることができました。
工具の交換頻度は、超硬チップソーが年間約50回以上であったのに対し、ダイヤチップソーは年間4回で済みました。
上記の削減率計算には、【工具交換に伴う人的コスト】までは含まれていませんから、ダイヤチップソーによる圧倒的な【作業効率の向上】をご理解いただけると思います。
この経験をされたお客様には大変な感謝をされ、『もう超硬工具には戻れない』、『他の工程にも横展開し、ダイヤ工具化を推進する!』とおっしゃっていただけました。
以上、夢のような話ですが、実際にあった話であり、このような事例があることも事実です。
最初にお伝えしましたように、ダイヤ工具に向かない被削材もありますし、ダイヤと超硬どちらでも切れるものの、コスト面・運用面・加工品質など、様々に比較すると超硬工具に軍配が上がることも多くあります。
超硬工具には超硬工具、ハイス工具にはハイス工具、ダイヤ工具にはダイヤ工具の、それぞれのメリットとデメリットがありますから、どのような結果が出るかは、実際に試してみなくては分からないというのも事実です。
当社は幾つかの実績や事例を持ち合わせておりますので、今お使いの工具のダイヤ工具化を、一度お試しになりませんか。
ぜひお客様の悩みや希望をお聞かせください。
当社はお客様と一緒になって考える提案営業を心掛けています。
お客様に最適な工具仕様や刃型の設計、ダイヤチップ(PCDチップ)の選定など、お客様個々のご事情に合わせたご提案をさせていただきます。
お問い合わせ・ご質問は、ホームページ内 【お問い合わせフォーム】 よりご連絡ください。心よりお待ちしております。
導入のご検討・ご相談はこちらから
ONLINE SHOP
既製品販売
オンラインショップにてご購入いただけます
MAIL FORM
お問い合わせ・ご相談
お見積りなど詳しいご相談は
お問い合わせフォームをご活用ください
TEL
053-421-9938
月〜金 9:00 - 17:00
(年末年始・祝日を除く)
Copyright© 小林ダイヤ All Rights Reserved.